Experience the versatility of plastic extrusion in design
Experience the versatility of plastic extrusion in design
Blog Article
A Comprehensive Guide to the Refine and Benefits of Plastic Extrusion
In the huge realm of production, plastic extrusion becomes a very reliable and vital procedure. Altering raw plastic into continuous profiles, it provides to a myriad of markets with its remarkable convenience. This guide intends to clarify the complex actions involved in this approach, the kinds of plastic apt for extrusion, and the game-changing benefits it offers the industry. The ensuing conversation assures to unfold the real-world impacts of this transformative procedure.
Recognizing the Basics of Plastic Extrusion
While it may appear complex initially glance, the process of plastic extrusion is essentially easy - plastic extrusion. It is a high-volume manufacturing method in which raw plastic is melted and shaped into a continuous profile. The process begins with the feeding of plastic product, in the kind of pellets, granules, or powders, into a heated barrel. The plastic is then melted making use of a mix of warmth and shear, used by a turning screw. When the molten plastic reaches the end of the barrel, it is required through a small opening called a die, shaping it into a desired kind. The designed plastic is then cooled down, strengthened, and reduced into desired sizes, finishing the process.
The Technical Refine of Plastic Extrusion Explained
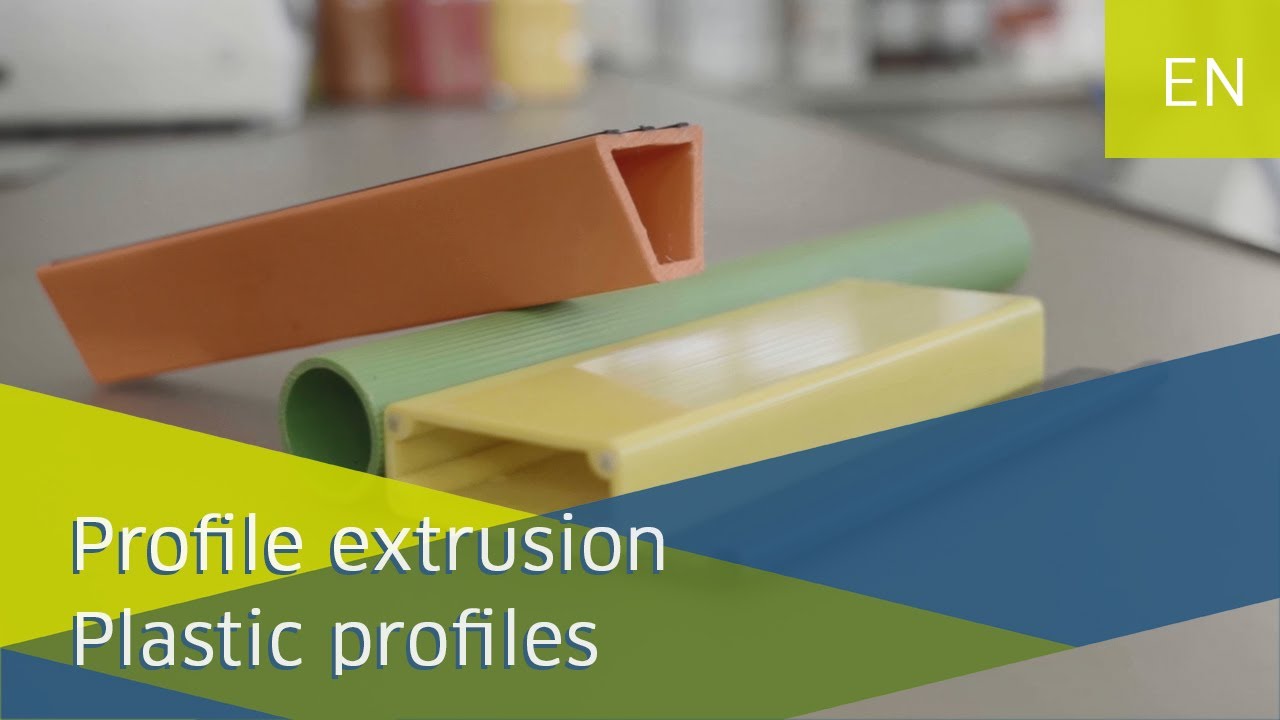
Kinds Of Plastic Suitable for Extrusion
The option of the best kind of plastic is an important element of the extrusion procedure. Different plastics supply special homes, making them more fit to certain applications. Comprehending these plastic kinds can substantially enhance the extrusion process.
Contrasting Plastic Extrusion to Other Plastic Forming Approaches
Comprehending the kinds of plastic suitable for extrusion leads the way for a wider conversation on how plastic extrusion stacks up versus other plastic developing approaches. These include shot molding, impact molding, and thermoforming. Each method has its one-of-a-kind uses and advantages. Shot molding, as an example, is outstanding for developing intricate parts, while impact molding is perfect for hollow items like containers. Thermoforming excels at creating huge or shallow components. Nonetheless, plastic extrusion is exceptional when it involves creating continuous profiles, such as gaskets, pipes, and seals. It likewise enables for a regular cross-section along the size of the item. Therefore, the selection of method mainly relies on the end-product requirements and specs.
Secret Advantages of Plastic Extrusion in Manufacturing
In the world of production, plastic extrusion uses many significant advantages. One remarkable benefit is the cost-effectiveness of the process, which makes it a financially link attractive production method. In addition, this strategy supplies exceptional product adaptability and improved production rate, consequently enhancing overall production effectiveness.
Affordable Manufacturing Technique
Plastic extrusion jumps to the leading edge as an economical production technique in manufacturing. This process attracts attention for its capability to generate high quantities of material promptly and effectively, giving makers with substantial cost savings. The key expense benefit is the ability to utilize much less expensive basic materials. Extrusion makes use of thermoplastic materials, which are much less pricey compared to porcelains or metals. Additionally, the extrusion procedure itself is relatively easy, lowering labor costs. Furthermore, plastic extrusion calls for much less energy than conventional production approaches, adding to lower operational expenses. The procedure additionally minimizes waste, as any excess or faulty products can be reused and reused, offering one more layer of cost-effectiveness. Generally, the economic advantages make plastic extrusion a very attractive option in the manufacturing market.
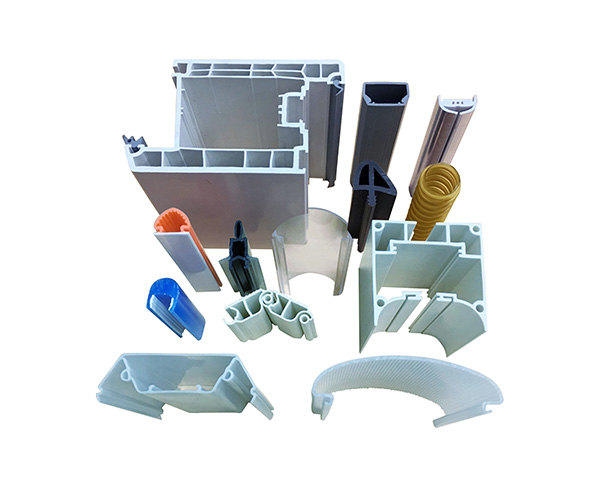
Superior Item Adaptability
Beyond the cost-effectiveness of plastic extrusion, one more substantial benefit in manufacturing lies in its remarkable item flexibility. This makes plastic extrusion a suitable remedy for industries that need tailored plastic parts, such as automotive, building, and product packaging. In significance, plastic extrusion's item flexibility promotes advancement while boosting functional efficiency.
Enhanced Production Rate
A check these guys out considerable benefit of plastic extrusion lies in its boosted production speed. Couple of other manufacturing procedures can match the speed of plastic extrusion. Additionally, the capacity to preserve consistent high-speed manufacturing without compromising item top quality sets plastic extrusion apart from other approaches.
Real-world Applications and Effects of Plastic Extrusion
In the world of production, the strategy of plastic extrusion holds extensive value. The financial benefit of plastic extrusion, mainly its high-volume and cost-efficient output, has actually revolutionized manufacturing. The industry is constantly aiming for advancements in eco-friendly and recyclable products, suggesting a future where the benefits of plastic extrusion can be kept without compromising environmental sustainability.
Conclusion
To conclude, plastic extrusion is a very reliable and efficient method of changing raw products right into diverse items. It pop over to this web-site supplies many advantages over other plastic creating approaches, including cost-effectiveness, high output, marginal waste, and style versatility. Its impact is greatly really felt in various sectors such as building and construction, vehicle, and durable goods, making it an essential process in today's production landscape.
Digging deeper right into the technical procedure of plastic extrusion, it begins with the option of the proper plastic material. As soon as cooled, the plastic is reduced into the called for sizes or wound onto reels if the item is a plastic film or sheet - plastic extrusion. Contrasting Plastic Extrusion to Other Plastic Forming Techniques
Understanding the kinds of plastic suitable for extrusion leads the means for a wider discussion on how plastic extrusion piles up against various other plastic developing approaches. Few various other production processes can match the rate of plastic extrusion.
Report this page